Ferrules: Stops
There are 2 material types of Stops:
Aluminum
Plain Copper
Aluminum Stops
Copper Stops
There are many different types and sizes of hand swaging tools.
Bench-Mounted vs. Hand-Type Swaging Tools
Bench-mounted swaging tools and hand-type swaging tools serve the same purpose of permanently connecting ferrules to cables using compression. However, they differ in their design and how they are operated:
Bench Type Swaging Tool
Hand Type Swaging Tool
Bench-Mounted Swaging Tools: | Hand-Type Swaging Tools: |
---|---|
|
|
Advantage Sales carries a wide selection of Hand Swaging Tools. Many are fitted with multiple cavities to cover a range of cable sizes. Download the Advantage Sales Catalog page on Swage Fittings and Hand Swaging Tools(opens in a new tab) below.
Cable Stops
Cable Stops are used at the very end of a Cable to stop the Cable from going through a hole or keyhole.
Example: 1/4″ Winch Cable with a Stop on one end and an eye with a hook on the other end. In the drum winch, you would place the Stop End into a keyhole slot in the drum winch and then reeve (wind) the cable onto the drum. It’d be much harder to keep the cable in place if there were no Stops holding that cable inside of the drum/keyhole.
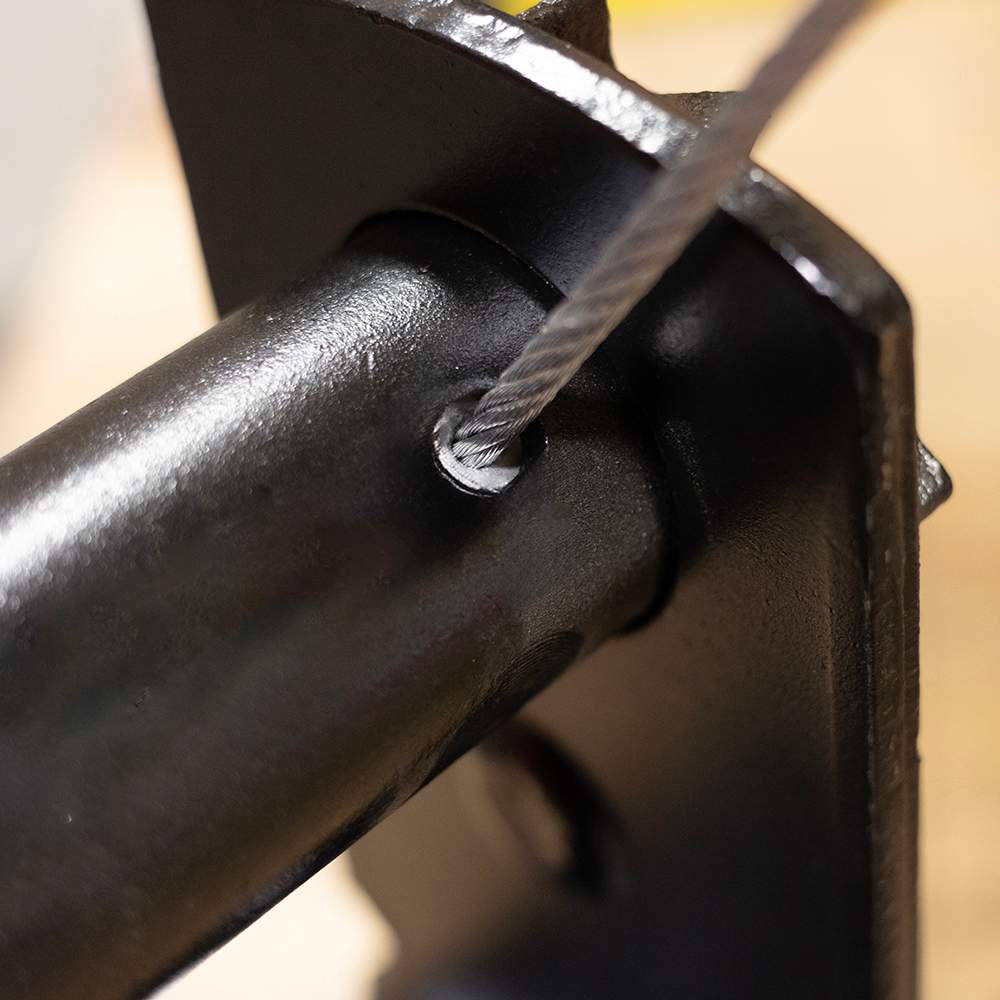
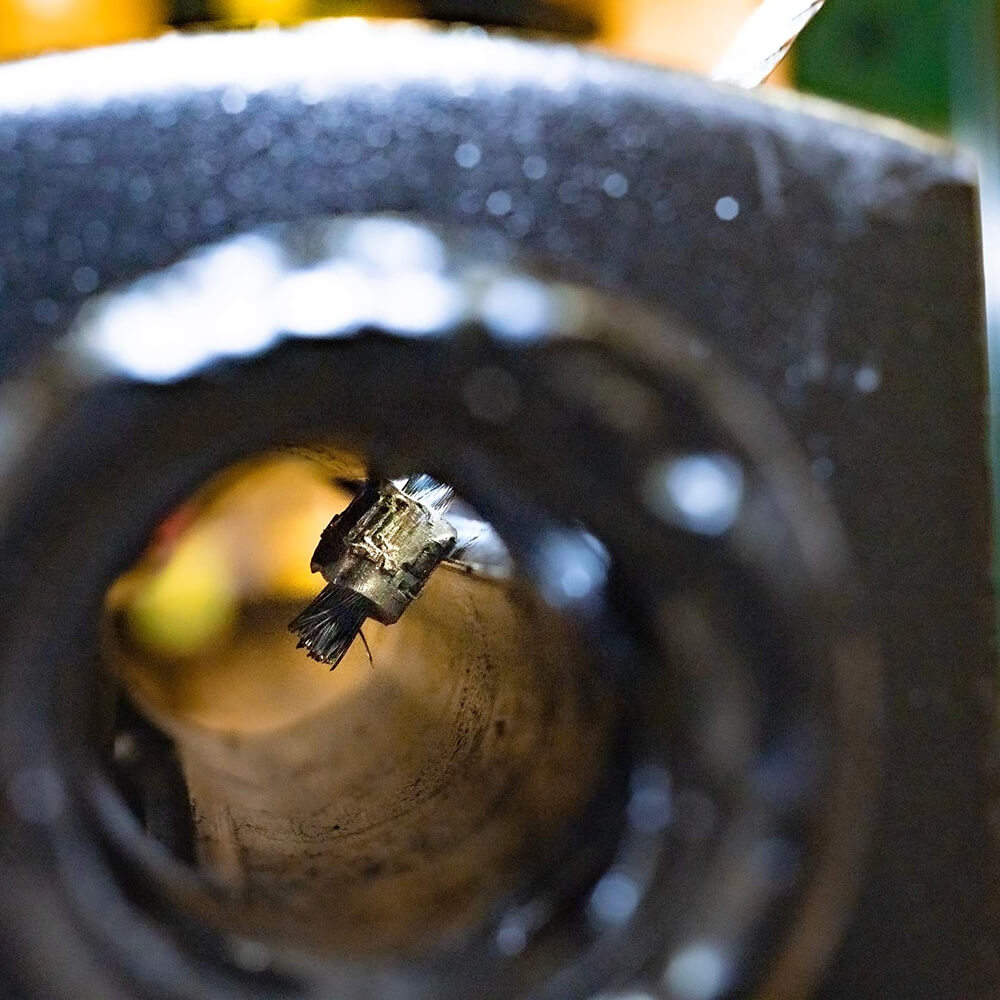
Learn to Properly Assemble Cable Stops
Below is a step-by-step guide to applying Cable Stops. Before we begin, It’s important to understand that Cable Stops applied with Hand Swaging Tools may need to use two separate size cavities on the swaging tool to achieve the proper after-swage dimensions. Begin swaging in the same-size cavity as your cable diameter. If the maximum after-swage dimensions are not met, size-down to the next smallest cavity and re-swage the stop until proper after-swage dimensions are achieved.
For the example below, we are using 1/8″ Aircraft Cable and a 1/8″ Aluminum Stop, which does not meet maximum after-swage dimensions in the 1/8″ cavity alone. Follow along in the guide below.
WARNING
- Stops are NOT for overhead lifting. Do not use assemblies made with stops for overhead lifting purposes.
- Failure to carefully read and adhere to these guidelines could result in severe injuries or death.
- Prior to installing sleeves, thoroughly review and comprehend these instructions.
- Ensure that stops are paired with cable of the same size.
- Follow the stops end termination procedures precisely as directed.
- Do not use stops above cable coated in plastic. Instead, remove the coating where sleeves will be swaged.
- Before usage, apply an initial load test to the assembly. This load should match or exceed anticipated operating loads.
General Info
8 General Facts about Stops & Sleeves
FACT 1
Aluminum is most commonly used on Galvanized Aircraft Cable. It is the most cost-effective type of Ferrule.
FACT 2
Sleeves and stops made from Stainless Steel, Plain Copper and Zinc Plated Copper materials are the only ferrules approved for use with Stainless Steel Aircraft Cable.
FACT 3
Due to being dissimilar metals, do not use Aluminum ferrules and Stainless Steel cable together. The use of Aluminum Sleeves on Stainless Cable is NOT safe.
FACT 4
Copper and Zinc Plated Copper Ferrules ARE able to be used with Galvanized Aircraft Cable. Some people prefer Copper Sleeves because they say that the Copper flows better into the cable. Our testing shows that if applied properly, both Aluminum and Copper Sleeves are safe.
FACT 5
When applying an Aluminum or Copper ferrule using a hand swager, always follow the guide picture above for hand swaging sequence.
FACT 6
Zinc Plated Copper is used in applications where the end user doesn’t want to see the Copper Ferrule turn green. Zinc plating doesn’t last forever, but it does offer some corrosion resistance.
FACT 7
Because Aluminum and Copper are both very soft metals, they can be applied in the field using a Hand Swaging Tool. There are several tools that are used to cover the entire size range.
FACT 8
Although Stainless Steel Sleeves are rarely used, they are still available from Advantage Sales. They need to be applied by a qualified sling making professional who has the proper hydraulic equipment and swaging dies. Please call an Advantage Sales team member for more information.